As technology advances and disrupts the manufacturing workforce and industry, it is becoming increasingly clear that businesses need workers who possess a mix of technical and non-technical skills to stay competitive.
Despite talent shortages and supply chain issues, the U.S. manufacturing sector is building back fast from the global pandemic. In June, U.S. manufacturing employment returned to pre-pandemic levels; demand for tech talent in the manufacturing industry doubled in the first five months of 2022 compared to 2021, according to job postings.
In this blog post we’ll explore how these hybrid jobs create new opportunities for businesses and employees alike – from improved process efficiency to enhanced collaboration across departments. As well as highlighting what organizations can do to ensure their workforce has the right skill set for today’s demanding work environment.
Why Are Hybrid jobs the Future of the Manufacturing Workforce
With the advancement of technology, the future of manufacturing jobs is changing. Hybrid jobs are becoming popular for companies, and for good reason. These jobs combine the skills of traditional manufacturing jobs with those of high-tech positions. In other words, a hybrid job requires both manual labor and technical expertise. This not only reduces the need for additional employees, it also allows for greater efficiency in the manufacturing process.
The integration of technology in manufacturing processes means that professionals with an understanding of automation, data analysis, and software engineering are increasingly in demand. These technical skills not only improve the efficiency of production but also have a significant impact on the industry itself. By integrating newer technologies, manufacturers can optimize their operations, reduce costs, and create products that better meet the needs of consumers.
Different Types of Hybrid Jobs Being Created in the Manufacturing Workforce
Industry Today’s analysis of job postings shows that manufacturers are looking to hire engineers to help them remain competitive in a rapidly evolving industry. Software Engineers and Principal Software Engineers easily topped the list of the most highly sought-after specialists in manufacturing, followed by Systems engineers, Electrical engineers, and Embedded Systems engineers. With manufacturers looking to collect, mine, and analyze data, it’s unsurprising that Data Scientists and Business Analysts also made the list of in-demand tech positions.
Some examples of these include hybrid jobs, like engineers with marketing experience, logistics personnel who also have engineering skills or data analysts with experience in quality control. By blending these skill sets, companies can benefit from employees who can seamlessly move between different areas of the production process, identifying and solving issues in real time. With the rise of technology in the manufacturing industry, these hybrid jobs are sure to become even more prevalent in the years to come.
An example of this is Software developers, one of the fastest-growing jobs in the manufacturing industry–software development is expected to expand 26% by 2031, giving it one of the highest expansion rates of any job. Although software developers may not be a traditional manufacturing job, they have an increasingly important role in the manufacturing industries.
Another example is Industrial Engineers, with a high projected growth rate of 10%. Among industrial engineering jobs, some of the industries with the highest growth include pharmaceutical manufacturing and electrical equipment manufacturing. Industrial engineers in the semiconductor manufacturing industry can also expect an impressive 20.3% increase in employment opportunities.
This highlights the importance of having a workforce equipped with technical skills, as it benefits the industry and contributes to a country’s overall economic growth. The need for technical skills in manufacturing is here to stay, and it’s imperative that businesses and governments invest in developing this talent pool.
5 Strategies to hire employees with both technical and non-technical abilities
Hiring employees is always a challenging and time-consuming task. However, it becomes even more complicated when you need to find candidates with a rare combination of technical and non-technical skills. Fortunately, there are several strategies you can use to ensure that you hire the right people for your organization.
- Consider using behavioral-based interview questions to assess candidates’ problem-solving skills and ability to work collaboratively.
- Look for candidates with a growth mindset who are willing to learn new skills and take on new challenges.
- Consider providing on-the-job training or mentorship opportunities to help employees develop skills that they may not have initially possessed.
- Emphasize the importance of cross-functional teams to promote collaboration and teamwork among employees with varying skill sets.
- Consider implementing a competency-based hiring model to help you identify candidates who possess a diverse range of skills and experience.
By using these strategies, you can increase your chances of finding the perfect employee with both technical and non-technical abilities.
Potential Hurdles for businesses that come along with these new roles and how to overcome them
As with any new role that businesses undertake, there are bound to be challenges and hurdles along the way. New roles often require cross-functional teamwork, which can pose difficulties for businesses that haven’t established clear lines of communication. Another hurdle is the volume of data that must be collected and analyzed to make informed decisions. The massive amounts of data can be overwhelming for businesses that are not equipped to handle it.
Another major hurdle is the skills gap within the manufacturing industry to accommodate these types of positions. According to a 2021 Deloitte study, the U.S. is expected to have 2.1 million unfulfilled manufacturing jobs by 2030 due to skill gaps. With technological advancements driving efficiency and productivity, companies are willing to pay top dollar for skilled workers who can help them stay competitive in the global market.
Hybrid jobs in the manufacturing sector are rapidly becoming the future of the industry. With an ever-changing landscape, companies are looking for employees that possess both technical and non-technical abilities to meet their needs. These new roles bring with them a wide array of unique benefits while also providing challenges that must be navigated.
However, those difficulties represent an opportunity for growth, especially if job seekers are to thrive in a future of hybrid jobs. As the demand for skilled workers is ever-increasing, it’s clear that these new roles will only continue to grow and evolve in the years ahead.
It’s essential that businesses and employees alike remain agile and willing to adapt as these positions become more commonplace and opportunities become available.
To learn more about the shifting manufacturing workforce check out our other blogs!
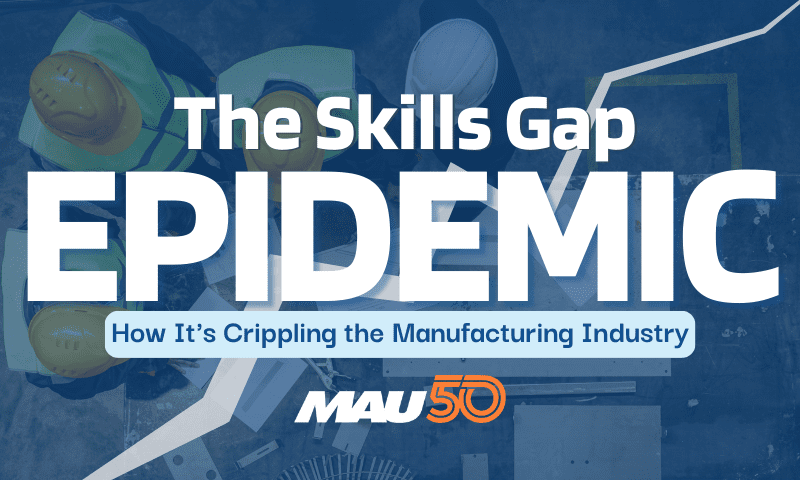