Consumer Products Manufacturer Meets Production Needs with Outsourcing Model
By strategically outsourcing non-core functions, focusing on critical activities, prioritizing employee safety, and realizing significant annual production savings, the division elevated its performance and achieved unparalleled success.
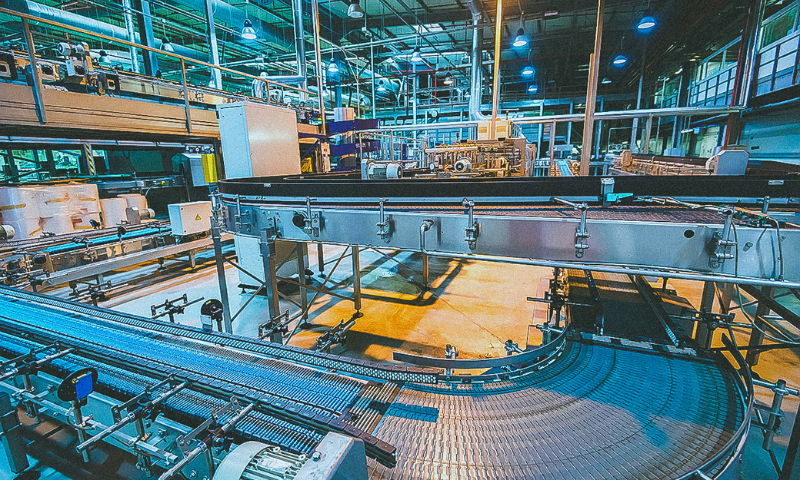
In a strategic move to enhance operational efficiency and focus on critical functions, a leading manufacturer partnered with MAU, an outsourcing firm, for the management of its daily responsibilities.
This partnership resulted in the reallocation of over 700,000 hours towards core operations within a single year. The case study explores the transformative journey of this manufacturing division, detailing how it achieved unprecedented success by outsourcing non-core functions, prioritizing employee safety, and realizing significant annual production savings.
Expansion Creates Packing and Logistical Challenges
In response to a significant increase in production demand, MAU Workforce Solutions partnered with a well-known consumer products manufacturer to tackle the mounting challenges faced by their specific division. With the successful delivery of five new machines, daily production jumped from six million to ten million products. However, this impressive growth necessitated a mill expansion, leading to packaging and logistical hurdles that needed urgent attention while still maintaining overall production goals.
The division’s internal team faced two main non-core functions that impeded their focus on other critical activities: raw material flow and operations process support. Recognizing the importance of these functions to the mill’s overall performance, the division sought an efficient solution that would allow their focus to be redirected toward production, engineering, and quality enhancements.
MAU Handles Pre- and Post-Production Processes
Drawing from their previous experience with MAU’s strategic temporary staffing and outsourcing services, the manufacturer collaborated with MAU to devise and execute a tailored outsourcing strategy. By combining core and non-core functions, the team was able to optimize their efforts and concentrate on vital production tasks. MAU demonstrated their commitment to understanding the mill’s existing processes and software and introduced Lean practices to streamline processes before and after the production of personal care products.
The scope of MAU’s responsibilities encompassed operational support, warehouse storage management, inventory confirmation, raw material allocation to operations, and palletizing finished products. The mill’s expansion also presented unforeseen challenges, including last-minute changes, special projects, and unexpected setbacks. In response, the manufacturer effectively utilized MAU’s dedicated staff, sparing internal employees from being pulled off the production line. This strategic decision not only ensured a quick reaction time but also resulted in cost savings.
By implementing an effective outsourcing strategy, this division of the consumer products manufacturer succeeded in overcoming the hurdles posed by their accelerated growth. Through their collaboration with MAU, they were able to streamline processes, optimize resources, and maintain their unwavering commitment to delivering high-quality products
Improved Efficiency, Safety, and Cost Savings
To streamline operations, the manufacturer made a strategic decision to outsource daily responsibilities to MAU. This enabled the reallocation of over 700,000 hours toward core functions within a single year. The resulting synergy propelled the division towards its desired objectives, fostering increased productivity while maintaining optimal resource allocation.
Within the colossal expanse of the mill’s 93,000-square-foot warehouse, MAU assumed the management of labor-intensive pre- and post-production tasks. This encompassed overseeing the operation of hundreds of stock-keeping units, autoloaders, and robotic palletizers. By expertly managing these non-core functions, MAU effectively liberated the manufacturer’s internal team to focus on high-value activities, expediting overall operations.
Recognizing the paramount importance of a safe work environment, the manufacturer sought the expertise of MAU’s outsourced safety training service. More than twenty high-risk positions were equipped with safe operating procedures, while individuals were diligently trained and certified in forklift operation and mill crisis management. The diligent implementation of these comprehensive safety measures resulted in a significant reduction in the OSHA Recordable Incident Rate, dropping from 11.4 to an impressive 2.14 over a span of four years.
One of the most notable benefits derived from outsourcing responsibilities to MAU was its substantial impact on the manufacturer’s bottom line. By harnessing the expertise of MAU’s skilled staff, the manufacturer achieved annual savings exceeding $220,000. This prudent financial strategy effectively avoided the need to rely solely on internal resources and instead maximized production output through a strategic partnership.
The collaboration between the manufacturing division and MAU showcased a remarkable case study in operational optimization. By strategically outsourcing non-core functions, focusing on critical activities, prioritizing employee safety, and realizing significant annual production savings, the division elevated its performance and achieved unparalleled success. This transformative journey serves as an inspiring testimony to the power of strategic decision-making and partnership in driving continuous improvement.