Tier 1 Automotive Supplier Fuels Efficiency By Outsourcing Production
Learn how MAU reinvigorated a Tier 1 Automotive Suppliers workforce to help them rollout a new production line.
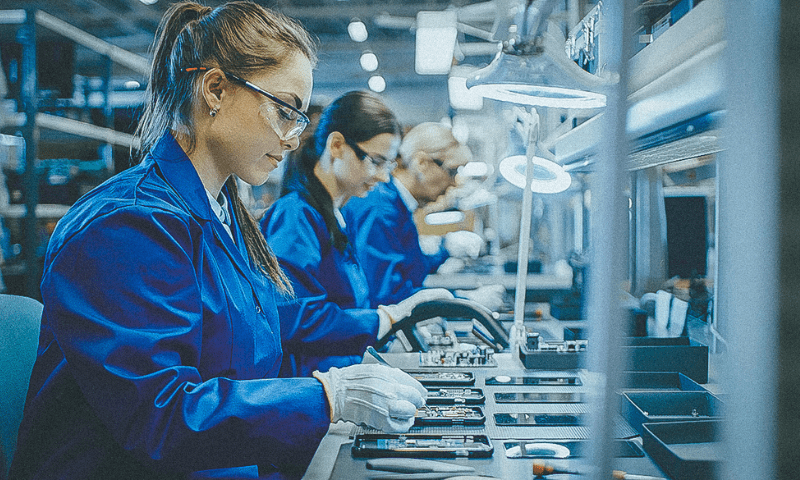
In the dynamic realm of automotive manufacturing, the importance of a skilled and agile workforce cannot be overstated. This case study explores the partnership between MAU Workforce Solutions and a prominent Fortune 500 industrial giant specializing in automotive systems manufacturing. Together, they tackled the challenge of scaling up production and introducing a new fuel injector line while optimizing existing operations to meet rising demand.
In response to growing market demands, the company’s plant embarked on an ambitious journey, expanding from an initial workforce of 105 to approximately 2,000 employees. Anchored by a commitment to quality and cutting-edge manufacturing processes, they achieved record production standards across their product range.
The Need for Expansion
To support the imminent launch of their new fuel injector line, the company sought to assemble a team of knowledgeable and experienced associates. This project required utmost precision and seamless coordination.
Additionally, maintaining strong production levels for their existing fuel injector line, which was already experiencing high demand, was crucial. The ultimate objective was to enhance stability, improve production, optimize quality, and implement a flexible business model to accommodate future growth and changes.
Specialized Outsourcing by MAU
Drawing from previous experiences and an astute understanding of the unique requirements at hand, the automotive supplier joined forces with MAU Workforce Solutions. Previous staffing approaches, involving temporary associates, were deemed insufficient in this scenario due to the need for specialized skills, experience, and workforce stability. MAU devised a tailored, results-driven, variable-cost solution specifically crafted to address the project’s intricate demands.
The MAU outsourcing team featured a comprehensive roster of key roles, including project managers, shift coordinators, setup mechanics, and production associates. These skilled professionals effortlessly managed project logistics, staffing, scheduling, training, and primary assembly line production, ensuring complete synergy between all phases of the endeavor.
Achieving Objectives:
Cost Reduction: As the project unfolded, outsourced services delivered remarkable savings of 68.9% on labor and operational costs. This strategy allowed the company to maintain a competitive edge as a low-cost supplier within the industry.
Enhanced Efficiency: With the core production team handled by MAU’s expert staffing and management, top-tier resources were seamlessly transitioned to the new, complex product line. The outcome was nothing short of exceptional, with both product lines showcasing outstanding levels of production, quality, and timely delivery.
Unparalleled Flexibility: MAU swiftly established hiring and training frameworks, enabling the rapid fulfillment of manpower requirements. This flexibility bolstered overall adaptability, empowering the company to successfully navigate the ever-evolving automotive landscape.
Through the targeted collaboration between MAU Workforce Solutions and the industrial giant, the company achieved monumental milestones in production line scalability, quality enhancement, and operational agility. This case study represents a testament to the power of innovative partnerships and strategic workforce planning in overcoming industry challenges and driving sustainable growth.