Tier 2 Automotive Supplier Implements Ongoing Workforce Solution to Meet Rising Product Demands
Read on to see how MAU’s Outsourcing experts created a custom solution for a growing Tier 2 Automotive Supplier.
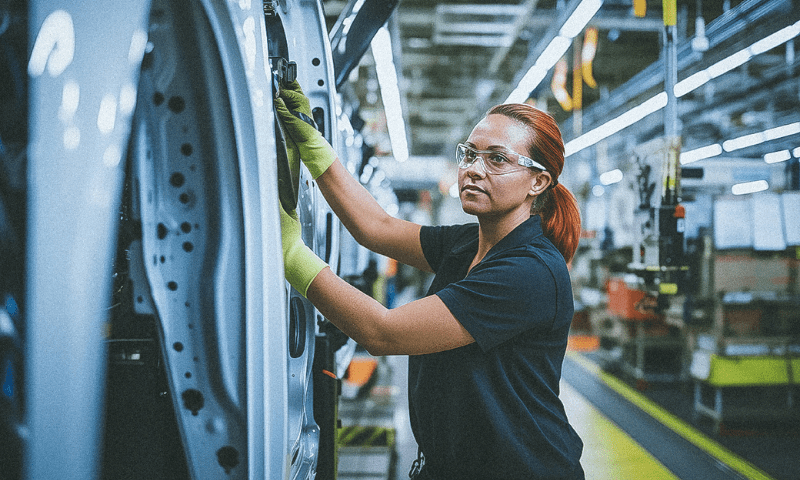
In the realm of automotive systems manufacturing, our esteemed customer, a Fortune 500 industrial giant known for their innovative solutions, has consistently pushed the boundaries.
Their remarkable growth trajectory has seen their workforce expand substantially from a modest 105 employees on their inception day to a staggering approximately 2,000 today. This phenomenal success can be attributed to their exceptional team of skilled workers and streamlined manufacturing processes, which have propelled their record production quality across various product lines.
The Challenge: Increased Demand and the Need for Production Ramp-up
As the demand for their commercial vehicle systems skyrocketed, one particular product witnessed an unprecedented surge in popularity within their facility. To meet this exponential demand, the company initially resorted to running the production line round the clock, merging second and third shifts.
However, the efficacy of this temporary solution was limited, and with optimistic projections indicating a further surge in demand, a sustainable and adaptable solution was imperative. The company sought a flexible approach that not only optimized production across the board but also streamlined the entire manufacturing process.
Together, they developed a comprehensive outsourcing solution that offered the desired flexibility. Under this arrangement, MAU associates not only managed day-to-day responsibilities but also provided additional skilled associates to accelerate the manufacturing process.
Implementation
The company’s product line supervisors were already dealing with a full workload, which made it challenging to train and manage additional team members. To address this, MAU took charge of managing, staffing, and training for specific functions within the production line.
They seamlessly integrated new associates into the existing team while ensuring smooth operations. The outsourced roles included contract managers, production supervisors, shift coordinators, and production associates dedicated to this particular product.
The Results
The collaboration with MAU yielded significant results for the company.
Improved Production: By outsourcing certain tasks, the company was able to efficiently handle a 27% increase in demand. Within a remarkably short span of thirty days, they ramped up production to maximum capacity and produced an additional 150,000 product units, surpassing initial expectations. This approach now allows them to consistently maintain their position as a low-cost supplier.
Enhanced Efficiency: With the support of MAU’s outsourcing team, the company could redirect their focus towards critical production functions such as shipping, expansion, and quality control. As a result, they achieved greater efficiency, even with the continued increase in demand.
Flexibility: MAU’s expertise enabled them to establish hiring and training parameters that facilitated the seamless integration of associates throughout the production process. This flexibility allowed the company to adapt to changing monthly production schedules while maximizing productivity.
This case study showcases the success of implementing a specialized outsourcing plan in the context of maintaining speed and performance in the running industry. By partnering with MAU, the company not only addressed their staffing challenges but also achieved remarkable results. The improved production, enhanced efficiency, and flexibility they experienced have positioned them as a key player in the market.