The global manufacturing industry is constantly evolving and adapting to new technologies, leading to a significant shift in the way processes are managed. With the introduction of advanced manufacturing techniques such as automation, artificial intelligence, and additive manufacturing, traditional methods of process management have become outdated.
This has not only revolutionized production processes but has also had a profound impact on overall operational efficiency and competitiveness for businesses worldwide. In this blog post, we will explore the significance of advanced manufacturing on process management and how it has transformed modern industrial practices for good.
But first things first, what exactly do we mean when we talk about advanced manufacturing? How does it differ from conventional methods? Most importantly, what impact does it have on process management?
How Advanced Manufacturing Has Changed Traditional Process Management
Advanced manufacturing has revolutionized the traditional process management approach, bringing about a paradigm shift in the way manufacturing industries operate. The integration of advanced technologies such as the Internet of Things, artificial intelligence, and robotics has paved the way for more efficient, cost-effective, and seamless manufacturing processes.
Companies can now design and produce customized products that meet specific consumer needs and preferences, increasing customer satisfaction. The use of data analytics enables manufacturers to analyze operations, track inventory, and optimize supply chain management, resulting in greater productivity and reduced waste.
With advanced manufacturing, businesses can achieve more streamlined processes and improved quality control, creating an overall competitive advantage in today’s global markets.
Impact of Advanced Manufacturing on Recruitment and Talent Acquisition
Advanced manufacturing has significantly reshaped the manufacturing industry’s recruitment and talent acquisition process. With the increased integration of cutting-edge technologies such as artificial intelligence (AI), robotics, and data analytics, there has been a notable shift in the required skill set. Although still valuable, traditional manufacturing skills are no longer sufficient to keep up with the evolving landscape.
As the industry embraces automation and digitization, there is a growing demand for specialized roles such as data analysts who can extract meaningful insights from the vast amount of data generated, robotics engineers who can design and optimize automated systems, and AI specialists who can develop intelligent algorithms to enhance manufacturing processes. These roles and many others now play a crucial part in driving innovation and efficiency in the manufacturing sector.
Recruiters are now faced with the challenge of sourcing candidates who possess not only industrial expertise but also a strong foundation in technology. The ideal candidates are those who are tech-savvy, adaptable to change, and capable of working seamlessly with complex machinery and software. Continuous learning and adaptability have become essential qualities in this rapidly evolving industry.
Moreover, the hiring process has transformed with the integration of AI technologies. AI-powered systems are now used to screen job applications, conduct initial interviews, and even onboard new staff. This streamlines and enhances the efficiency of the recruitment process, allowing recruiters to focus on more strategic tasks.
The integration of advanced manufacturing techniques has not only revolutionized the jobs within the industry but has also transformed the entire recruitment and talent acquisition landscape. It has created new opportunities, redefined skill requirements, and brought forth the need for a workforce that is technically skilled and adaptable to ever-changing technological advancements.
The Role of Technology and Data in Supporting Advanced Manufacturing
Technology has become critical for driving operational excellence and business success in today’s complex and dynamic manufacturing landscape. By leveraging advanced manufacturing processes and embracing cutting-edge technologies, companies can significantly improve their production efficiency, quality, and competitiveness.
From automated systems and machine learning algorithms to blockchain-enabled supply chains and augmented reality toolkits, there is no shortage of technology solutions available to support modern manufacturing operations. But the real value of technology lies in its ability to enhance process management capabilities, enabling manufacturers to capture data, generate insights, and optimize workflows in real-time.
Data plays a crucial role in decision-making processes for manufacturing leaders. As advanced manufacturing techniques give rise to unprecedented data, leaders are increasingly harnessing this information to make informed decisions that drive operational efficiency and business growth.
The integration of data analytics provides leaders with real-time insights into their operations, enabling prompt identification of issues and opportunities for improvement. By analyzing production efficiency, quality control, and supply chain management data, decision-makers can determine where optimizations can be made and strategically allocate resources.
With data at their fingertips, manufacturing leaders can make decisions based on empirical evidence rather than relying solely on intuition or previous experience.
Transformation of Production Process Management through Advanced Manufacturing
The advent of advanced manufacturing has led to a radical transformation of production processes. Automation and robotics have taken center stage in production lines, reducing human intervention and, subsequently, the likelihood of errors. Machinery equipped with sensors and connected via the Internet of Things (IoT) can autonomously monitor and control operations, increasing efficiency and precision.
Moreover, plant managers can proactively adjust production outcomes through real-time data collection and analysis. Predictive maintenance, facilitated by machine learning algorithms, allows for timely detection and prevention of equipment failures, enhancing operational consistency.
The incorporation of augmented reality on the plant floor has also bolstered training and troubleshooting procedures, allowing for a more interactive and immersive experience. By overlaying digital information onto physical objects, staff can visualize complex procedures, conduct virtual equipment inspections, and resolve issues more efficiently.
Advanced manufacturing has transformed production processes, driving unprecedented productivity, accuracy, and quality. This progress signifies a new era of manufacturing, where technology and digitalization streamline operations and pave the way for a more sustainable and efficient industry.
The future of process management is undeniably intertwined with the advancements in manufacturing processes. Advanced manufacturing is deemed the game-changer as technology continues to escalate and revolutionize the manufacturing industry. Its potential for continued growth is limitless, and the benefits it brings to process management are unprecedented.
With automation, data analytics, and IoT, advanced manufacturing is creating a smarter and more efficient production ecosystem that delivers optimal results. This shift not only enhances the bottom line but also fosters a workforce of skilled labor and increases the overall competitiveness of organizations.
As we venture into the future, it’s certain that advanced manufacturing will remain an integral component and a driving force for process management.
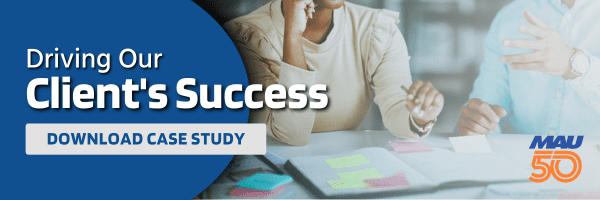