The global landscape of manufacturing is in a relentless pursuit of innovation. Technologies such as artificial intelligence, robotics, and advanced data analytics are propelling the sector into unprecedented realms of efficiency and productivity and changing workforce development as we know it.
Shifting demands call for new skills, new perspectives, and a continuous process of training and retraining. This challenge is not just a company-level concern; it’s a sector-wide imperative that, if unaddressed, can stifle growth and impact competitive standing.
In this blog post, we’ll dissect the multifaceted challenges that the manufacturing sector faces in molding its workforce to meet the demands of advanced technology. From understanding the current state of affairs to charting innovative solutions, we will explore the terrain of workforce development in advanced manufacturing.
The Current Workforce Landscape in Manufacturing
Technology’s Onslaught and Its Impact on Jobs
The integration of advanced technologies such as 3D printing, Internet of Things (IoT), and machine learning stands as a testimony to the industry’s power to innovate. But with innovation comes transformation. Since passage of the IRA, close to 200 new clean technology manufacturing facilities have been announced—representing US$88B in investment—which are expected to create over 75,000 new jobs. The rise of automation, for instance, has raised pertinent questions about job displacement and skill obsolescence.
According to a report by McKinsey & Company, about half of all work activities worldwide could feasibly be automated using currently demonstrated technologies. While this doesn’t imply mass unemployment, it does underscore a pressing need for workforce adaptability and future-proofing.
Strategic Workforce Development Under the Microscope
The current trends in workforce development point to a vigorous reevaluation of traditional practices. Continuous learning, remote training, and agile skill development have emerged as strategic imperatives for manufacturers. The ability to forecast skills demands and align workforce capabilities accordingly has become non-negotiable in the battle for market relevance.
Leading companies in this arena are abandoning the one-size-fits-all model, recognizing that personalized development plans are more effective in nurturing talent. They are also investing heavily in apprenticeship programs, collaborating with educational institutions, and expanding internal training platforms to build a pipeline of skilled workers.
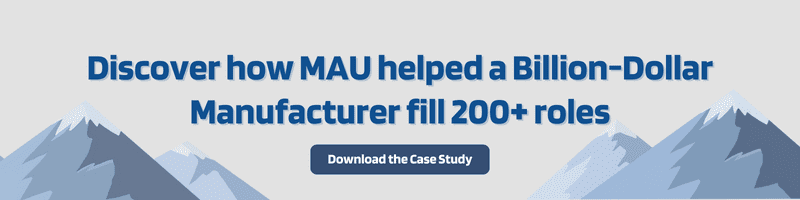
Key Workforce Development Challenges
Perhaps the most critical challenge in workforce development is the notorious skills gap. As the industry accelerates towards advanced manufacturing processes, the chasm between the skills workers have and those the industry needs is widening.
The skills most in demand encompass technology proficiency, problem-solving, and a fundamental understanding of data insights. The fastest growing roles between 2022-2032 are for statisticians, data scientists, engineers, logisticians, computer and information systems managers, software developers and industrial maintenance technicians.
Attracting and Retaining Talent in the Age of 4.0
Competition for skilled labor is fiercer than ever. Attracting and retaining the right talent demands a strategic HR approach that goes beyond competitive wages. It involves creating a workplace culture that values innovation, invests in employee growth, and champions work-life balance.
In a recent survey conducted by the National Association of Manufacturers (NAM), almost three-quarters of surveyed manufacturing executives feel that attracting and retaining a quality workforce is their primary business challenge.
Organizations that succeed in this arena often have comprehensive talent management programs that identify and nurture high potential employees. These programs, combined with transparent career progression pathways, not only attract top talent but also retain them in the long term.
Navigating the Aging Workforce Dilemma
The phenomenon of an aging workforce presents unique challenges for the manufacturing sector. The loss of institutional knowledge and experience cannot be overstated. Companies must deal with the imminent retirement of the workforce’s most seasoned members while transferring their knowledge to younger employees.
Gen Z now makes up a significant portion of the global workforce, in 2030, we’ll see Generation Z constitute about 30% of the workforce. This group brings a new set of skills and expectations to the table, which will impact how industry leaders approach workforce management.
Future Outlook and Recommendations
The future of workforce development in advanced manufacturing holds both challenges and opportunities. The emergence of smart factories, with their interconnected systems and data-driven operations, will necessitate a new breed of digital-savvy workers. Companies must adapt not only to changing demand but also to the ways in which work itself is organized and executed.
The next decade will witness a significant shift in the very concept of a skilled worker, with adaptability, IT proficiency, and a mindset for lifelong learning becoming the new benchmarks.
Addressing the workforce challenges that loom over the manufacturing industry is not a task to be taken lightly. It requires a concerted effort from all stakeholders – companies, workers, educational institutions, and governments. The need of the hour is innovation in policy, practice, and outlook. It is a call for the industry to rise to the occasion, to craft a workforce as resilient and responsive as the technologies they wield.
In the end, the success of manufacturing in the age of advanced technology will be measured not just by the efficiency of its tools, but by the skill, adaptability, and engagement of the people who wield them. The challenges may be formidable, but so is the human spirit for ingenuity and progress. It is a new manufacturing era, and the workforce is the heart that will propel it forward.
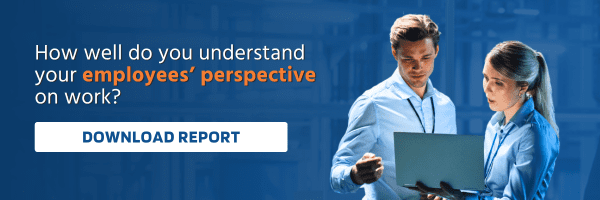